فهرست مطالب
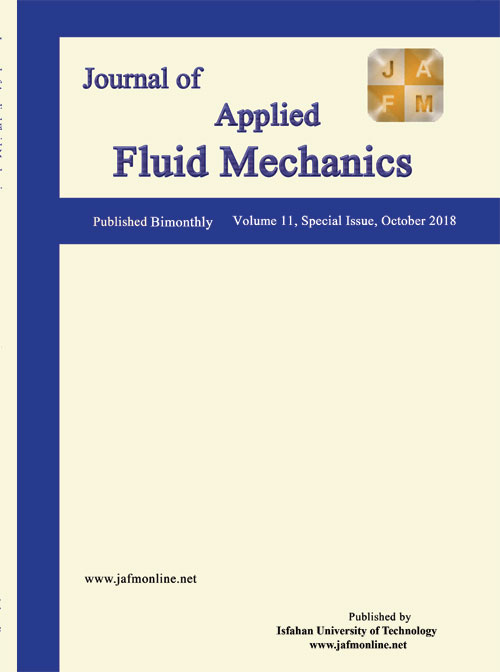
Journal Of Applied Fluid Mechanics
Volume:11 Issue: 5, Sep-Oct 2018
- تاریخ انتشار: 1397/07/18
- تعداد عناوین: 20
-
-
Pages 1-5The use of biodiesel as an alternative diesel engine fuel is increasing rapidly. However, due to technical deficiencies, they are rarely used purely or with high percentages in diesel engines. Therefore, in this study, we used butanol as an additive to research the possible use of higher percentages of biodiesel in a diesel engine. B100 (100% biodiesel) was prepared as the baseline fuel. Butanol was added to biodiesel as an additive by volume percent of 5% ,10%,15% 20%(denoted as B95 but5, B90 but10, B85 but15 and B80 but20), were used in a single cylinder, four strokes direct injection LHR engine. The effect of test fuels on brake specific fuel consumption, brake thermal efficiency, exhaust gas temperature, and NOX, smoke opacity emission was investigated. The experimental results showed that the performance and emission of LHR engine we can use of the 100% biodiesel. Besides, the exhaust emissions for B80 but 20 were fairly reduced.Keywords: Biodiesel, LHR engine, Performance characters, Emission characters
-
Pages 7-14Desirable thermal properties of nanofluid is the vital reason for using nanofluid. There is an exemplary development in various applications using nanofluid. Mathematical and experimental models were developed to predict the thermal properties of nanofluids, the models are tiresome and expensive and have discrepancies between them. Soft computing tools are most useful in prediction, classification and clustering the data with good accuracy and with less expensive. In this paper, comparative analysis of Multi Layer Perceptron (MLP) model and Support Vector Regression (SVR) model were done by using various evaluation criterions. The two models developed to predict the thermal conductivity ratio of CNT/H2O and the results were compared. The present modeling has been carried out using MATLAB 2017 b. In both the models, the experimental values and predicted values possess good accordance. Regression coefficient value (R2) for overall data is 0.99 and 0.98 for MLP and SVR models respectively. The Root Mean Square Error (RMSE) value is less in MLP model when compared with SVR model, RMSE values are 0.01578 and 0.01812 respectively. The prediction is best in MLP model but with limited experimental data set, it fails to address over fitting problem, whereas SVR model is ideal with limited data set, it overcomes over fitting problem and possess better generalization than MLP model.Keywords: Nano fluids, Thermal conductivity, Artificial neural network, Multilayer perceptron, Support vector regression
-
Pages 15-21The implications of Internal Combustion (IC) Engines are complex now a day in a fast living technical field. Much work have been done on IC engines to enhance their performances with engine modification, alternate fuels, fuel supply system, combustion system and cooling systems. However every trial has its own merits and demerits. In particular, reaching the limit of conventional coolants. In this investigation, so called novel fluids MWCNT nanofluids at 0.1, 0.3, and 0.5%volume concentration are taken as IC engine coolant to study its performances and compare with the performances of water. The test is performed at five electrical loadings and by keeping flow rate of coolant 300 LPH as constant. It is found that the mechanical efficiency is enhanced by 13 to 24%, the Break thermal efficiency increases by 9-21%, the TFC reduces 9-19%, and the exhaust temperature of the engine decreases by 5-10% at 0.3% vol. concentration of nanofluids. The 0.3% nanofluids found to have better performance while compared with water at the same engine conditions.Keywords: Conventional fluid, Nanofluid, Stability, Load, Performance
-
Pages 23-29In this experimental work, heat transfer and pressure drop analysis of a Double helically coiled tube heat exchanger by using Multi-walled carbon nanotube (MWCNT) /Water nanofluid as a coolant. The analysis is done under constant heat flux and turbulent flow condition. The double helically coiled tube heat exchanger (DHCTHX) is designed and fabricated. The MWCNT/water with 0.2% 0.4% & 0.6% volume concentration nanofluids are prepared by using two-step method. The nanofluid prepared is characterized by using SEM (Scanning Electronic Microscope). Initially, hot water and cold water with 120,140,160& 180LPH (liter per hour) of flow rates are tested. Secondly hot water and 0.2% 0.4% & 0.6% volume concentration of MWCNT/water nanofluid with the same mass flow rates are tested. On comparing, the MWCNT nanofluids have better heat transfer rate than that of water. It is found that the heat transfer rate increases with increasing volume concentration of nanofluids. The maximum heat transfer rate obtained is at 0.6% volume concentration of nanofluids at the 120LPH mass flow rate at 1460 Dean Number. It is also studied that MWCNT /water nanofluid’s overall heat transfer rate is 56% higher than water at 0.6% nanofluid at 1460 Dean Number. It is also found that the pressure drop of MWCNT/water 0.6% nanofluid is 49% higher than that of water at 1460 Dean number.Keywords: MWCNT-water, Double Helically coiled tube heat exchangers, Nusselt number, Thermal conductivity, Secondary flow, Dean number
-
Pages 31-37In this paper, a new optimization method coupling genetic algorithm (GA) and computational fluid dynamics (CFD) based on Windows Socket was found to optimize the configurations of porous insert in a tube for heat transfer enhancement. The region in the enhanced tube was divided into several layers in the radial direction. The porosity of porous media filled in each layer was the design variable, which varies from 0.5 to 1.0. The results show that the thermo-hydraulic performance of the enhanced tube can be improved effectively by using the optimized porous insert, particularly using the optimized multiple layers of porous insert. However, there is an appropriate layer number of porous insert to ensure the optimal performance of the enhanced tube for a given set of parameters.Keywords: Heat transfer enhancement, Porous insert, Genetic algorithm (GA), Computational fluid dynamics (CFD), Optimization
-
Pages 39-44Hybrid fuel for the operation of diesel engine is the motivated research in this study. The diesel engine is modified to operate with the hybrid diesel and compressed natural gas (CNG). In this work a four stroke, single cylinder diesel engine is considered to operate at variable load and speed. At is operation condition the emission characteristics are measured to model the proposed Manhattan K-nearest neighbor (MKNN) technique. The MKNN is modelled to effectively analysis and predict the torque, brake power, exhaust emissions and break specific fuel consumption (BSFC). The MKNN is modelled with the constant K=3 and applied Manhattan distance formula for neighbor determination. From the result analysis it is evident that the proposed MKNN technique can effectively predict the engine performance and exhaust emission while the usage of hybrid fuel.Keywords: Hybrid fuel system, Compressed natural gas, Manhattan K-Nearest Neighbor, Manhattan distance, Diesel engine emission
-
Pages 45-52The integrated circuits face a huge issue to meet out the cooling demand due to the rapid development in technology. Several researchers have investigated the different possibility of cooling medium to improve the heat dissipation in an integrated circuits. Heat sink is a kind of thermal heat transfer device used to dissipate heat from an integrated circuit (IC) to surrounding due to low cost and reliability in heat dissipation. In this numerically work, the electronic chip with the heat sink is analyzed to study about the cooling rate, surface temperature of the chip, reliability and power dissipation of the chip with different heat transfer medium, fin height and fin thickness. The different heat transfer medium is air, water and engine oil. The ANSYS (v12) fluent software is used to study numerically about the electronic chip cooling. In this research work, the heat transfer rate of water is 9.5% greater than air and 1.4% than engine oil at the same Reynolds number is obtained. The power dissipation is increases up to 1.45% of the fin height 55mm and heat transfer rate is enhanced by increasing the fin thickness up to 2.10% in 6mm. However, the lifetime of the electronic chip with fin height 55mm is 2.06% hrs (day) greater than the fin with 35mm. It is observed that the electronic chip with water as a heat transfer medium with proper fin height and thickness is highly reliable to enhance the heat transfer than that of air and engine oil.Keywords: ANSYS-Fluent, Heat sink, Nusselt number, Fin height
-
Pages 53-61Refrigerants are the basic working fluids in refrigeration, air conditioning and heat pumping systems. The development of refrigeration and air conditioning industry depends to a large extent on the development of refrigerants to suit various applications and the development of various system components. At present the industry is dominated by the Vapour compression refrigeration systems, even though the Vapour absorption refrigeration systems have also been developed commercially. A number of climate-friendly alternatives to CFC/HCFC/ HFC refrigerants are, or will become, available for use in commercial refrigeration applications. Alternatives available today include hydrocarbons-isobutene (R-600a), propane (R-290), and propylene (R-1270) -ammonia (R-717), and carbon dioxide (R-744) respectively. This research focused to develop a strategy of refrigerants to improve the efficiency of the refrigeration system. The proposed methodology consists of Linde-Hampson refrigeration system operated with blends of hydrocarbons propane (R290) and butane (R600) as the low-temperature working fluid. To improve the efficiency of the system an evolutionary machine learning hybrid lightning search algorithm-simplex method (LSA-SM) is proposed in the study to forecast the refrigerant temperature and pressure at different ambient temperatures and loading conditions. LSA-SM has higher computational accuracy, faster convergence rate, and stronger stability than other algorithms and can effectively solve the problem of constrained nonlinear optimization in reality. The proposed methodology is mathematically modelled and executed in the running platform of Mat Lab and executed as performance charts.Keywords: Linde- Hampson refrigeration system, Vapour absorption refrigeration systems, Hybrid lightning search algorithm-simplex method (LSA-SM), Mat Lab
-
Pages 63-67It has been posted as a challenge for the researchers to identify an alternate fuel source for the petroleum fuels. This had become a major concern as the harmful pollutants are being produced in the exhaust of engines. The present works aims at the suitability study of esterified pine oil blended with diesel fuel as a replacement of diesel in an unmodified CI engine. The direct pine oil is a source obtained from agriculture. It has the innate characters like high viscosity, high calorific value and low cetane number values. It was found that esterified pine oil blended with diesel fuel could be successfully used with acceptable performance and better thermal efficiency. From the experimental investigation it is found that by blending pine oil with diesel, brake thermal efficiency can be increased up to 25%, friction power can be reduced by 4 kW. All the emission were observed to be low for the blended samples. The major contents like CO2 and NOx were decreased by 30%. It is suggested to replace the diesel with pine oil blend for applications with low friction power and will thus help in achieving energy economy and rural economy development.Keywords: Pine oil, Performance, Emission, Corrosion test
-
Pages 69-74Modern civilization is much dependent on fossil energy. Energy obtained from fossil resources is much higher than any other resources. The petroleum based fuels are highly contributing to environment pollution. With greater environmental concerns and long term sustainability point of view, it becomes necessary to develop alternative fuels with properties comparable to petroleum based fuels. Biodiesel is the suitable option for transportation vehicles. Vegetable oils are considered as good alternatives to diesel as their properties are close to diesel and able to reduce the net CO2, HC and NOX emission. This paper is aimed at the study of the performance and emission characteristics of direct injection diesel engine fueled with blends of diesel, linseed oil and cottonseed oil as fuel. The experiment was conducted with various blend proportions of biodiesel at different engine loads. It was found that BMEP, Indicated thermal Efficiency, Brake thermal efficiency and Specific fuel consumption is slightly maintained at base fuel performance. The main factor is emission of CO2, unburnt hydrocarbons, NOx and EGT were less compared with base fuel however, and smoke density and CO were slightly increased.Keywords: Biodiesel, Transesterification, Linseed oil, Cottonseed oil, Performance, Emission
-
Pages 75-78The technology of co-firing was used to study the combustion of groundnut shell and coal at three different ratio of biomass (10%, 20%, and 30% in weight) and combustion of miscanthus and coal at three different ratio of biomass(10%,20%,30%) using thermo gravimetric analysis (TGA). When compared to firing of coal, the co-firing of coal and biomass (groundnut shell, miscanthus) has shown a good combustion result. The ignition temperature (Ti) burnout temperature (Tf) is reduced in the co-combustion when compared to the combustion of coal alone. The best blend ratio of coal/groundnut shell is 80%/20%. The best blend ratio of coal/miscanthus is 70%/30%.Keywords: Groundnut shell, Coal, Thermo gravimetric analysis, Co-combustion study
-
Pages 79-89In this paper a new attempt is made by optimization of welding parameters in welded butt joint the Hybrid LM25 Aluminium Metal Matrix Nano Composite Cylindrical Rod Samples. Here Hybrid LM25 Aluminium metal matrix nano composite (AMMNC) is made by using stir casting method. Here Base metal LM25 Aluminium alloy is adding the reinforcing matrix as 2% of nano Silicon carbide particles along with 3% of nano alumina for producing Hybrid AMMNC Samples. Joining of this Hybrid AMMNC samples are done by using TIG welding, due to its low cost and good quality of welds among arc welding processes these reinforcements are dispersed as nano particles to get a benefit of enhancing in their strength. While joining of hybrid AMMNC cylindrical rod butt joint by using TIG welding process. To optimize the TIG welding parameters such as Welding pulse current, Arc voltage and Shielding gas flow rate experiment is designed using One-Factor Multilevel-Categorical Factor technique. By conducting the experiment, effect of welding parameters such as welding pulse current, Arc Voltage and shielding gas flow rate on weld centre micro hardness is evaluated. Regression equation is developed using Design-Expert version 11 statistical software to predict the weld centre micro hardness. Correlation co-efficient (r2) showed 0.95 and error % showed less than 5% which means the regression equations are developed in the most consistent. Empirical model is developed to optimize the pulsed current parameters of welding is also performed using Design Expert - statistical software. Optimized values for pulse on welding time, arc voltage and shielding gas flow rates are 120A, 21V and 12 l/m respectively. Optimized predicted value of weld centre micro hardness has been observed as 100HV. Trial runs are performed for optimized PCTIG welding condition to check the consistency of the model, which resulted only 5% of deviation between experimental values and predicted values. It shows the optimized welding pulsed current, Arc Voltage and Shielding gas flow rate parameters resulted in higher micro hardness value which implies that strength of the weld is increased with respect to optimize welding parameters. In addition to investigate the temperature distribution in optimized Hardness value of welded AMMNC sample. Then heat fusion in the size and distribution of heat source, the travel speed, the heat conduction in the welding direction and the surface heat loss during welding are considered. A numerical scheme is developed to solve the three dimensional problem. With the help of a mathematical model, the effect of welding parameters such as heat input of the weld, preheating of the work piece and moving velocity of heat source on weld penetration in welded AMMNC cylindrical rod samples are discussed. The steady-state temperature profiles of the welded AMMNC samples are solved by finite difference method. In addition, a thermal experiment such as Heat Flux Differential Scanning Calorimeter Experiment is conducted to verify the theoretical results and Numerical results in ANSYS software. The predicted values from the proposed model are compared with the experimental data of optimized welded AMMNC samples.Keywords: LM25 Al Metal Matrix Nano Composite Cylindrical Rod (AMMNC), Tungsten Inert Gas Welding (TIG), Silicon Carbide (SiC), Nano Particle (np)
-
Pages 91-101This study describes the enhancement of thermal performance of heat pipe using SiO2 and TiO2 nano fliud. The study explains about the effects of heat pipe inclination and heat input on the thermal efficiency and thermal resistance. Heat pipe is an advance type of heat exchanger which transfers huge amount of heat due to the effect of capillary action and phase change heat transfer principle. Recent developments in the heat pipe with high thermal conductivity through nano fluids. This paper reviews, influence of various factors such as heat pipe tilt angle, charged amount of working fluid, nanoparticles type, size, mass/volume fraction and its effect on the improvement of thermal efficiency, heat transfer capacity and reduction in thermal resistance. The nano fluid preparation and the analysis of its thermal characteristics also have been reviewed.Keywords: Nano fluids, Heat pipe, Inclinations, Thermal resistance, Thermal efficiency
-
Pages 103-105Natural ventilation methods are far more efficient than the counter modern artificial methods and also it needs no energy for the ventilation. In this proposed system, angle of air flow at the entry is changed and it results in Air change per Hour (ACH) and the age of air changes. In accordance with the earlier studies, it has been concluded that there is a significant impact due to geometrical configuration in the wind catcher. Density of the air also supports this ventilation method, as cold air settles down due to high density and the hot air escapes through the top of the opening due to its lighter density. During this work, wind catcher’s openings is altered in several angles for the improvement in the distribution of air. The evaluation is based on i) Downward air flow due to wind entry ii) Upward air flow due to temperature gradient. Geometry of the testing room is 3.3m X3.3mX3.3m. The CFD results are validated based on upward air flow due to temperature gradient using the simulation software ANSYS. In the inlet openings, aperture angles such as 30degree, 45degree, 60degree and 75degree are tested. Results are approached analytically and to support analytical result simulation results are compared for better air velocity and uniform distribution.Keywords: Ventilation, Window capture, Computational fluid dynamics, Less energy consumption
-
Pages 104-114Experiments have been carried out on a single cylinder, four stroke, and variable compression ratio diesel engine to investigate the effect of compression ratio on its performance, combustion and emission parameters, when it is fuelled with Spirulina of 20%, 40%, 60% and 80% blend with standard diesel. The parameters that were measured comprised of performance parameters such as Brake Power (BP), Brake Thermal Efficiency (BTHE), Brake Specific Fuel Consumption (BSFC), Mechanical Efficiency, along with Combustion parameters such as Cylinder Pressure and Net Heat Release Rate (HRR). The exhaust gas emission included Carbon Monoxide (CO), Carbon dioxide (CO2), Nitrogen oxides (NOX) and Hydrocarbon (HC). The results obtained for Spirulina at compression ratios (CR) of 15, 16 and 17.5, at different loads have been compared and analyzed to that of standard diesel. After analyzing the data, it is evident that while fuelling the engine with spirulina biodiesel, there is a clear decrease in the emission of Carbon monoxide, Nitrogen oxides and Hydrocarbons. And the performance characteristics of the engine remain unaltered. The optimum engine performance was found at higher compression ratio.Keywords: Spirulina algae, Compression ratio, Performance, Combustion, Emissions, Diesel engine
-
Pages 115-119Radiators are heat exchangers used to transfer thermal energy from one medium to another medium. In the existing plain fins type radiator are commonly used, which are usually set up in a cross flow arrangement made up of aluminum and copper alloy. Powerful fan and water pump is accompanied in this to greatly improve heat dissipation rate. For higher cooling capacity of radiator, addition of fins is one of the approaches to increase the cooling rate of the radiator. This method follows the principle of increasing contact surface. Contact surface can also be increased by varying fin geometrical structure. In this project simple modification has been carried out in the existing fin geometry with a view to improve its heat dissipated rate. The varying fin structures are Box type, Sharp type, Round type. Sharp type radiator fins is fabricated to evaluate the effectiveness of the radiator. Also comparison of conventional coolant with SiC Nano fluid has been carried out by using Solid works and Ansys software. The result are compared with both analytical and experimental fin design is concluded.Keywords: Fins, Heat transfer, Geometrical, Coolant, Nanofluid
-
Pages 121-128From the past few decade, many manufacturing industries are using heat exchangers for reducing the energy consumption and hence reducing the fuel costs. Most widely used types of heat exchangers in industries are Double Pipe Heat Exchangers and Shell & Tube Heat Exchangers. It is recently that industry people and researchers are becoming more aware of the advantage of using Spiral Heat Exchangers for heat transfer between two different fluids.A Spiral Heat Exchanger is formedby a coiled sheet arrangement with two channels coiled one around the other. The distance between the sheets is kept constant to maintain the area of cross section through out the spiral path of the channels. In this work, flow pattern and heat transfer in a Spiral Heat Exchanger are analyzed using a couterflow model geometry. The results obtained for the fluid flow and heat transfer gives an idea about how we can optimize the flow rate of the fluids thus increasing the efficiency of the heat exchanger.Keywords: Heat exchanger, Computational analysis, Geometric modelling, Flow analysis, Fluid structure interaction
-
Pages 129-134From the past many decades, mesh generation posed many challenges in the field of computational sciences for many researches. High rise in computational power has enabled many researches to tackle the problems of complex geometries. Due to the high need of computational power, computational cost also increased abruptly. In today’s world, many academic and industry researches are willing to increase the use of present simulation technology; mesh generation plays a vital role in this aspect. we can say that many real-world simulation problems are dependent on mesh generation which has more chances in giving an inaccurate simulation results. In order to make the simulation process simpler, Meshless methods are introduced to the field of Computational Fluid Dynamics. This technique requires a less computational power compared to the computational power needed for generating the mesh. In the present dissertation, our main objective is to develop a scheme for Meshless method for the field of Computational Fluid Dynamics for flow over a blunt body. The performance of the present scheme is evaluated by comparing the simulation results with existing experimental data and also compared with the results obtained by generation of mesh using commercial CFD software.Keywords: Lagrangian interpolation, Meshless coding, Flow simulation
-
Pages 135-139In this present work, a heat exchanger test set up is configured as a closed circle framework comprising of a storage tank (14 litres), a pump, a detour line, heat exchange test area, a water cooler and a flow meter. Numerical investigations is carried out using computational fluid dynamics (CFD) on a device was comprising a basic channel with rectangular cross area utilizing water as the working liquid. The influence of geometry and flow parameters on the pressure drop across the radiator tube test section is investigated. Inlet winglets were utilized as a part of the present numerical study. The goal of the present numerical study is to understand the impact of these inlet winglets set inside the car radiator tubes, on the general heat exchange performance of the radiator. The calculations were carried out on a finite volume based code ANSYS fluent15.0, with one, two and three winglets set toward one side mass of the tube, at three different Reynolds numbers and with three winglet configurations set on every one of the end of the tube, at five distinctive Reynolds numbers. It is observed for the experimental results and CFD values heat the optimum number ribbed winglets for the pressure configurations is two and three gives a temperature rise of 10c and its pressure drop of 20.10 Pa.Keywords: Winglets, Heat transfer coefficient, Radiator tube, CFD
-
Pages 141-150Air conditioning is widely used in many areas to reduce the heat and humidity of the work place and to maintain a room temperature for thermal stability and physical ability to perform various tasks. Computational Fluid Dynamics (CFD) is based on the numerical solutions of the fundamental governing equations of fluid dynamics namely the continuity, momentum and energy equations. Computerized fluent mechanics is one of the increasing paradigm in the air flow simulation in vehicle designs. The design optimization of vehicle can offer better efficiency in cabin surface as well as aerodynamic. In vehicles, air conditioning tends to offer efficient thermal conditioning and air circulation inside the cabin for passenger comfort from different climate variation. Almost all the automobiles available in the market are fitted with air-conditioning systems. The manufacturers focus clearly on the AC system for a wide variety of climates. As technology advances, AC system is also adhering major advancements. In general, automobile air-conditioning systems are designed to provide comfort for the driver and the passengers during a journey. The conventional electrical-driven compression systems are widely used in almost all of the automobiles today. An air-conditioner is operated to make a hot and humid passenger compartment a more comfortable environment. However, with the improvement in vehicle fuel economy, the allowable power consumption for the air-conditioner has been decreasing, in relation to the overall power consumption of the vehicle. The internal temperature-humidity conditions are an essential factor for the comfort and health of passengers, and also for the safety of drivers. In this research, the air conditioning inside vehicle cabin is analyzed. The objective of the research is to develop an air depression design inside the top surfaces of the rear cabin. The optimal flow of air inside cabin increases the thermal comfort of the vehicle. The proposed cabin depression design inside the rear top surfaces are analyzed under thermal variation and airflow circulation inside the cabin. The Ansys fluent tool is utilized in this paper to evaluate the variation of air flow and the temperature inside the passenger vehicle cabin respectively. From the research analysis, the proposed evaluation of the depression design is more optimal for air conditioning in budgetary small passenger vehicles.Keywords: Automobile, Air conditioning, Humidity, Air duct, Temperature, Vehicle cabin, ANSYS Fluent