فهرست مطالب
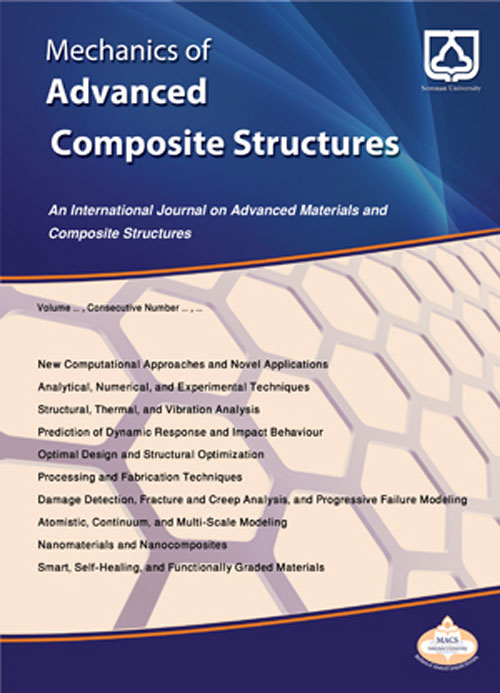
Mechanics of Advanced Composite Structures
Volume:6 Issue: 2, Summer and Autumn 2019
- تاریخ انتشار: 1398/08/10
- تعداد عناوین: 16
-
-
Pages 75-80High velocity oxy-fuel (HVOF) is one of the emerging technologies among the thermal spraying techniques, for producing uniform and dense coatings, having high hardness and very low porosity. A NiCrBSi alloy coating was prepared with approximately 400µm thick, on the A516 steel by means of HVOF and was analyzed with regard to its detailed microstructures, phase formation, thickness, roughness and microhardness. The obtained coating was crack-free, mechanically bonded to the substrate and had very low porosity. A microhardness tester was used so as to determine the mechanical properties of the coating. The microstructure of the coating and its phase transformations was characterized using scanning electron microscopy (SEM), X-ray diffraction (XRD) and energy dispersive spectroscopy (EDS), respectively. The major crystalline phases involve Cr3NiB6, Ni31Si12, Ni4B3, Ni3B compounds and Ni-γ solid solution. Also, amorphous phase was obtained in the coating. The results indicated that coating microhardness values were in the range of 700-800 Hv and a uniform distribution of different elements was observed.Keywords: NiCrBSi coating, Hardness, Morphology
-
Pages 81-94The present study aims to investigate the analysis of stress, strain, displacement, and electrical potential of a thick hollow cylinder made of FGPM under mechanical and thermal loads. Distribution of mechanical property of material is considered along the shell stick through the power distribution function. Thermal loads have been taken to signify the difference of temperature between outer and inner surfaces for each type of mechanical property. After extracting and solving the differential equations in transient state and the observation of mechanical and thermal boundary conditions, governing functions are obtained through the following parameters: thermal conduction non-homogeneous parameters, thermal linear distribution coefficient, elastic stiffness constant, piezo-electric coefficient, and dielectric constants.Keywords: Piezo-electric, FGPM, Hollow cylinder, Transient, Thermal Stress
-
Pages 95-104The present article investigates the elasto-thermodiffusive interactions in a transversely isotropic elastic medium in the context of thermoelasticity with one relaxation time parameter and two relation time parameters. The resulting non-dimensional coupled equations are applied to a specific problem of a half-space in which the surface is free of tractions and is subjected to time-dependent thermal and chemical loadings. The analytical expressions for the displacement components, stresses, temperature, strain, mass diffusion, and chemical potential are obtained in the physical domain by employing the normal mode analysis as a tool. These expressions are calculated for a copper-like material and the results are depicted graphically. A comparative study of a diffusive medium and a thermoelastic medium show that diffusion has a significant effect on the thermophysical quantities. Furthermore, in the absence of the effect of thermodiffusion, the results agree with the existing literature.Keywords: Generalized thermoelastic diffusion, Finite wave speed, Normal mode analysis, Transversely isotropic material, Green-Lindsay model
-
Pages 105-115In this study, discrepancies between the free vibration of fiber-metal laminate (FML) and composite cylindrical shells reinforced by carbon nanotubes (CNTs) based on Love’s first approximation shell theory have been considered by beam modal function model. The representative volume elements consist of three and four phases for composite and FML structures, respectively, which include fiber, CNTs, polymer matrix and metal for FML cylindrical shells while the metal section is ignored for composite cylindrical shells. The modulus of carbon nanotubes reinforced composites cylindrical shell could be defined based on rule of mixture. In addition, the fiber phase can be reinforced by the obtained matrix using the extended rule of mixture. The frequencies of FML and composite cylindrical shells reinforced by CNTs have been compared to each other for different materials, lay-ups, boundary conditions, axial and circumferential wave numbers.Keywords: Free vibration, FML, composite cylindrical shells, CNTs, Beam modal function model
-
Pages 117-129In the present work, thermo-electro vibration of the piezoelectric nanoplates resting on the elastic foundations using nonlocal elasticity theory are considered. In-plane and transverse displacements of the nanoplate have been approximated by six different modified shear deformation plate theories considering transverse shear deformation effects and rotary inertia. Moreover, two new distributions of transverse shear stress along the thickness of the nanoplate were introduced for the first time. The equations of motion were derived by implementing Hamilton’s principle and solved using analytical method for various boundary conditions including SSSS, CSSS, CSCS, CCSS and CCCC. Based on a comparison with the previously published results, the accuracy of the results was confirmed. Finally, the effects of different parameters such as boundary conditions, variations of the thickness to length ratio, aspect ratio, increasing temperature, external voltage, foundation coefficients and length scale on the natural frequency of the plate were shown and discussed in details.Keywords: Analytical method, Elastic foundation, Piezoelectric nanoplates, Nonlocal theory
-
Pages 131-138Graphene sheets are combined of Honeycombs lattice carbon-carbon bonds which have high natural frequencies, high strength, and high conductivity. Due to important applications of the graphene sheets particularly at higher frequencies, the study of their dynamic behavior is important in this frequency range. From Molecular Dynamics (MD) point of view as the dimensions of graphene sheet incline, the number of atoms increases, and as a result, its modeling becomes more time-consuming. Besides the experimental methods in small dimensions are difficult to conduct and not economical. In this research Finite Element Method (FEM) is used for frequency analysis of graphene sheets in various dimensions in order to study the capability of FEM in simulating the dynamic behavior of graphene sheets at small scales. In this research, the objective function is to find the minimum size of the sheet in which both methods have good convergence. Also, the time-consuming for the simulation is investigated. The time-consuming for analysis in the Finite Element Method is less than other methods, including Molecular Dynamics (MD), Generalized Differential Quadrature (GDQ), etc. Also, The results indicated that for circular single-layer graphene sheets simulation, using Finite Element Method (FEM) is in good agreement with the results obtained from the Molecular Dynamics (MD) simulation, in the radius more than 100 nm. In this research, the ABAQUS has been used for Finite Element Method (FEM) simulation.Keywords: Graphene, finite element method, Frequency Analysis
-
Pages 139-146This article presents the investigative work conducted on the fracture toughness and microstructure of Al6061-9% graphite particulate composites. The requisite specimens for the fracture toughness testing were compact tension ones prepared using stir casting technique. The Al6061-9% graphite particulate metal matrix composite has been heat treated in the underaged condition. It is observed from the results that as aging time increases, the fracture toughness increases. This gain in fracture toughness is with the loss of ductility. Examination of the fractured surface of Al6061-graphite is done using a scanning electron microscope (SEM) which shows the brittle fracture of the composite.Keywords: Al6061-9%graphite, Fracture toughness, Age hardening, CT specimens, SEM
-
Pages 147-158Due to considerable stored energy in surfaces of nano-scales in comparison with the stored energy in their bulk, considering the surface energy is necessary for the analysis of various behaviors of nano-scales for more precise design and manufacturing. In this article, the longitudinal dynamic behavior of nanobars in the presence of the surface energy parameters is studied. To this end, the longitudinal dynamic behavior of nanobars is modeled based on the simple theory. To consider the effects of the surface energy parameters, the surface elasticity theory is used. In addition, the nonlocal elasticity theory is implemented to capture the size effect. Then, the governing equation of motion and corresponding boundary conditions are derived from Hamilton’s principle. The governing equation becomes the inhomogeneous cause of considering the surface energy parameters while in none of the previous researches like the investigation of transverse vibration of nanobeams and torsional vibration of nanobars, the surface energy parameters would not cause inhomogeneity of the governing equation. Due to inhomogeneity of the governing equation, the homogeneous case is firstly solved, and frequencies and mode shapes of nanobar are obtained for fixed-fixed and fixed-free boundary conditions. Then, using the modal analysis method and Duhamel’s integral, the inhomogeneous governing equation of motion is solved, and the overall dynamic response of nanobar is reported.Keywords: Nanobar, Surface energy, Nonlocal elasticity theory, Longitudinal dynamic behavior, Simple theory
-
Pages 159-165In the present study, the effect of banana peel and bagasse particle additives on the friction and wear behavior of multi-ingredient friction material nanocomposites have been investigated. In order to develop optimized properties of friction nanocomposite, the type and content of natural additives were changed beside the constant amount of other constituents such as alumina nanoparticle and other functional ingredients. The microstructural investigation and wear test were performed. The results showed as the natural additive content increases, the density of nanocomposite, and the hardness decrease. The highest hardness and friction values and the lowest specific wear rate would be achieved for a composite sample with 5 wt. % of baggase additive.Keywords: Friction Materials, banana peel, Bagasse, brake pad, asbestos free
-
Pages 167-179In this article, an exact analysis of compressors spool in a turbojet engine has been investigated. The spool is modeled as a rotating thick-walled hollow circular cylinder with free-clamp ends. It is subjected to centrifugal load due to its constant rotational speed, uniform internal and external radial loads and arbitrary thermal gradients. The analysis is initially investigated for the homogeneous state. Then FGM state is investigated to improve the safety factor of the spool. In order to calculate the safety factor, Von-Mises criterion has been used. In FGM state, thermoelastic properties of material would vary in radial direction. The function of these properties changes is assumed exponential. To obtain the highest safety factor, the numerical optimization method has been used and the optimal results have been compared with the homogeneous state. To drive the relations for free-clamp ends boundary condition, at first spool is considered clamp-clamp ends. Then, the effect of releasing one of the ends has been calculated and finally, using the principle of superposition, the results for clamp-free ends state has been investigated. In addition, the effect of changing the non-homogeneous coefficients, spool rotating speed, radial loads and thickness on the safety factor are investigated. Increasing the thickness and radial loads would lead to a change in the optimal coefficient and would result in reducing the safety factor of optimum state. The results showed that utilization of FGM state with optimal coefficient could significantly increase the safety factor and reduce displacements. Furthermore, increasing the rotation speed and radial loads would result in a change in the optimal non-homogeneous coefficient and reduce its equivalent safety factor.Keywords: Turbojet Engine, Compressor Spool, Thermoelastic Analysis, Functionally Graded Material
-
Pages 181-190
Using natural hemp fibers to reinforce the tensile characteristics of polymer matrix composites is investigated in this article. The fibers were applied to the epoxy matrix in unidirectional and hybrid tissue forms. After preparation of standard tensile stress test specimens via manual layup, the standard tensile test was done. Young’s modulus, ultimate tensile stress, and the amount of absorbed energy before fracture were obtained experimentally. A comparison is performed with respect to fibers posture. In all cases, the tissue fiber samples gave a higher strength in comparison with the unidirectional laminated fibers. An analytical model is finally presented to estimate the elasticity modulus of the tissue reinforced composites.
Keywords: Natural hemp fibers, Polymer-matrix composites, Strength, Mechanical testing -
Pages 191-200Steel composites reinforced with alumina nanoparticles were prepared by powder metallurgy process. Samples containing two different amounts of carbon (0.35 and 0.55 wt.%) and 0-5 wt.% Al2O3 nanoparticles were fabricated by mixing, compacting and sintering of diffusion bonded Distaloy AE powder. The density, hardness and wear tests were performed on the prepared samples. Furthermore, the microstructures and worn surfaces were analyzed by optical and scanning electron microscope (SEM), respectively. The wear tests were carried out in forces of 30, 40 and 50 kN and 1000 m distance in dry condition and ambient temperature. The results showed that increasing the alumina nanoparticles would reduce the density (~ 10.8 and 9.6 % for 0.35 and 0.55 wt.% C, respectively) and would increase the hardness (~ 14.1 and 7.2 % for 0.35 and 0.55 wt.% C, respectively) of sintered samples. With increasing carbon content, the amount of lost material and the rate of wear decrease. The lost volume increases with increasing wear distance and applied force. Addition of reinforcement to the steel matrix, improves the wear resistance up to 3 wt.% alumina nanoparticles. This increase in the samples varies between 30% to 73%. More increasing of alumina (5 wt.%) decreases the wear resistant of samples. The wear mechanisms including oxidation in low forces that convert to adhesive and abrasive with increasing applied force. The wear curves indicate that as the wear distance increases, the lost volume increases, while the wear rate decreases.Keywords: Sintered Steel, Nanocomposite, Nano-reinforcement, Alumina, Wear Behavior
-
Pages 201-223A new closed form formulation of three-dimensional (3-D) refined higher-order shell theory (RHOST) to analyze the free vibration of composite circular cylindrical shells has been presented in this article. The shell is considered to be laminated with orthotropic layers and simply supported boundary conditions. The proposed theory is used to investigate the effects of the in-plane and rotary inertias as well as transverse normal and shear strains on the dynamic response of thick composite cylindrical shells. The trapezoidal shape factor of the shell element is incorporated to obtain accurate stress-resultants. Using Hamilton’s principle, the equations of motion are obtained and solved in terms of the Galerkin method. Numerical results for the natural frequencies are verified by making comparison with the 3-D exact elasticity iterative solutions in the literature. In addition, the validity of the results is further verified by ABAQUS. According to the results, for thick composite cylinders with large length-to-radius and orthotropic ratios, through thickness exact integration yields accurate stress-resultants for proper prediction of the natural frequencies.Keywords: Free vibration, Higher-order shear deformation theory, Trapezoidal shape factor, Circular cylindrical shells, Composite
-
Pages 225-237In this article, the effects of different foam production times and temperatures on the mechanical, physical, and structural properties of polypropylene (PP) foam has been investigated. The microcellular PP foams were carried out using supercritical carbon dioxide (sc-CO2) as a physical foaming agent in a batch process. The samples were placed in a pressure vessel and were saturated with sc-CO2 at room temperature (23 - 25 °C) and saturation pressure of 40 MPa for 35 hours. Then, samples were removed from the vessel after releasing the pressure and were immersed in a glycerin bath for different times of 90, 180, and 270 seconds and different temperatures of 155 °C, 165 °C, and 175 °C. The mechanical responses of samples, e.g., flexural, Izod impact, and dynamic mechanical thermal properties, and physical characterization containing water absorption and relative density, were studied. Scanning Electron Microscopy (SEM) was applied to investigate the surface morphology. The cell size, cell density, and cell structure of PP foams were investigated by morphological parameters. X-ray diffractometer was utilized to evaluate the interaction effect on the samples. Results showed that in the semi-crystalline polymers such as polypropylene, the foaming temperature must be higher than the melting temperature of PP. A simultaneous examination of mechanical, physical, and morphological test results as well as cell structure properties indicate that the best temperature and time conditions for producing PP foams are the temperature of 175 °C and time of 270 seconds, respectively. These optimum conditions could be used in the industrial production of PP foams.Keywords: Polypropylene, Microcellular foam, Mechanical properties, Foaming conditions, Physical foaming method
-
Pages 239-247In the present work, an experimental study was done to prepare Acrylonitrile-Butadiene-Styrene matrix composite reinforced by Nano-silica particles. The hot extrusion method was utilized here to fabricate the composite specimens used for flexural and compression tests. In order to identify the effect of SiO2 content and extrusion temperature, 12 experiments have been carried out and the obtained results were discussed according to scanning electron microscopy (SEM) images of the sample cross section. In addition, crack propagation and barreling phenomenon were discussed by variation process factors. Obtained results revealed that addition of nano-SiO2 up to 3% would cause the improvement in both flexural and compression strengths while a further increase in reinforcement content causes reduction of composite strength. Furthermore, samples prepared at extrusion temperature of 210°C, have lower strength compared to those fabricated by 180°C temperature. Finally, it was found that increase in SiO2 content and decrease in extrusion temperature would increase the brittleness of composite.Keywords: Acrylonitrile Butadiene Styrene, Nano-silica, Extrusion, Compression, Flexural
-
Pages 249-261A new type of composite structure with a metal foam is reinforced by the metal corrugated core, called metal-foam-filled sandwich panel with a corrugated or V-frame core, is modelled, simulated, and studied in this article. All types of samples with different relative densities of the foam are tested and analyzed under the drop hammer load. The sandwich panel included two aluminium face-sheet, aluminium foams, and aluminium corrugated or V-frame cores. Mathematical and finite element models were also been developed to predict the effects of the relative density of the foam and other geometric parameters on the energy absorption. In addition, the mathematical equations based on a mass-spring-damper problem with two degree-of-freedom (DOF) were derived to evaluate the kinetic and kinematic parameters of the sandwich panel, such as velocity, acceleration, contact force, and energy absorption. It was found that the models could represent the dynamic response of the sandwich panel. Finally, in order to improve the performance of the sandwich panel, an optimization method was utilized for finding the optimum parameters which play an important role.Keywords: sandwich panel, Corrugated core, Metal Foam, Mathematical model, Optimization method