فهرست مطالب
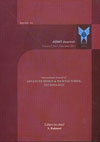
International Journal of Advanced Design and Manufacturing Technology
Volume:13 Issue: 3, Sep 2020
- تاریخ انتشار: 1399/06/11
- تعداد عناوین: 11
-
-
Pages 1-8Indentation forming is an internal tube forming process in which a mandrel with a diameter slightly larger than that of the tube is pressed inside the tube and in so doing, creates the internal profile. Forming forces have a significant effect on the spring back, residual stress, quality of the inner surface, quality of tube dimensions, and tool wear. In this study, the forming process of CK45 steel tube by carbide tungsten tool in the presence of ultrasonic vibration has been simulated and the effect of ultrasonic on the forming mechanism has been investigated by introducing two regimes according to the forming conditions. The effects of tool feed-speed and amplitude of vibration on forming force reduction have been investigated. According to the simulation results, the main reason for the force reduction in the presence of longitudinal tube ultrasonic vibration is the intermittent phenomenon which is the continuous or impulsive regime. The critical amplitude which determines the borderline of continuous and impulsive regimes is obtained 38µm by the simulation of the process. The maximum force reduction obtained in continuous regime is 64.2% at the critical amplitude. The simulation results are consistent well with the previous experimental data.Keywords: Finite Element Method, Indentation Tube Forming, Intermittent Phenomenon, Ultrasonic Vibration
-
Pages 9-20
Development of effective sound insulators for interior noise reduction of vehicle cabin is an essential phase of the process of vehicle manufacturing. One of the main issues in this process is the space limitations for packaging the firewall insulators. In this paper, a new approach in sound insulator optimization will be used, in which the space limitation has been considered. The insulator consists of a Micro-Perforated Plate (MPP) and a limp porous layer. MPP layer is suitable for use in vehicles due to low weight and flexibility in design. The main goal of this study was to reach better performance and less weight and volume in a specific thickness. So, a mathematical model of this sound package has been developed and validated by experimental data and SEA software. The simulation results illustrate the high performance of the optimized sound package in practical application, particularly at higher frequencies. On the other hand, the weight and thickness of the optimized sound package are less than the conventional sound packages. These qualities provide an optimized design that has better compatibility with the automotive industry.
Keywords: Absorber, Genetic Algorithm, Micro-Perforated, Optimization, Sea, Sound Package -
Pages 21-31
In this paper, different geometries and arrangements of vortex generators for improving the heat transfer performance of heat sinks have been studied. The effect of different parameters including the inclination angle of vortex generators and the distance between them are also investigated on heat transfer performance of heat sinks. Numerical computations are done based on the finite volume method and they have been validated with available experimental data which were in accurate compatible with each other with RMSE error of less than 6%. According to the obtained outcomes, between rectangular, triangular and symmetrical NACA0012 vortex generator, heat sink with NACA0012 vortex generator has the best thermal performance. On the other hand, heat sink with rectangular vortex generator has the highest fluid flow pressure drop. So, using rectangular vortex generator with heat sink needs a fan with the highest power. Also, the results show that thermal resistance of the heat sink decreases with Reynolds number increase. Also, heat sink pressure drop increases with Re number enhancement. Meanwhile, the pressure drop rate is more sensible in higher Reynolds numbers.
Keywords: Computation Fluid Dynamics, Heat sink, heat transfer, Vortex generator -
Pages 33-49
Performance and improvement of flight efficiency at various velocities for flight systems, in particular, rotorcrafts, with specific complexities in motion and its nonlinear equations are always of particular interest to researchers in the aerial and control domains. In this research, a new control algorithm is addressed based on the complete nonlinear Unmanned Rotorcraft (UR) model and its four main inputs. Exploiting state feedback and Polytopic Linear Parameter Varying (PLPV) modeling and using Linear Matrix Inequality (LMI), the velocity control problem is investigated. The trim points of the system are produced under different velocity control conditions. State feedback control gain matrix which plays a main role in producing the ultimate control signal, is computed by solving a set of LMIs under various conditions. Finally, instead of using a Nonlinear model, a Polytopic model is used for controller synthesis. With this goal, different scenarios for the proposed flight velocity control (in different dynamic ranges, minimum velocity to maximum velocity) are implemented. The simulation results demonstrate a very good performance of the proposed controller in the basis of PLPV modelling. It can be concluded that the proposed manner is useful to overcome the disruptions imposed on the flight system due to the changes in the equilibrium points and the uncertainties of the parameters and/or possible errors due to the unwanted possibilities in the system.
Keywords: Nonlinear Unmanned Rotorcraft, LMI, LPV, Polytopic Modelling -
Pages 51-57
In recent decades, the use of aluminium alloys is developed in the automotive industry with regard to the need for lightweight and anti-corrosion components, one of which is AA7075 Al alloy. In this study, the multi-step deep drawing process of AA7075 aluminium sheets under various blank holder forces is investigated through a numerical simulation and is then validated with experimental results. Simulations were conducted by ABAQUS finite element software, and the influences of the blank holder force on the wrinkling height, rupture occurrence and thickness distribution of the sheet were studied. The optimum amount of blank holder force at each drawing step is determined so that the height of wrinkling, and the thinning percentage do not exceed the permissible value. Based on the results, the blank holder force magnitude should be considered descending during the four successive steps to achieve more uniform thickness distribution, and also the wrinkling height could be reduced by increasing the blank holder force in the analysed force range. The optimum amount of blank holder force in the four drawing steps was 28000, 2500, 1500 and 600 N, respectively. In general, the minimum thickness was created in the corner of the punch. The results also showed that an excessive increase in the blank holder force in order to eliminate the wrinkling caused the thinning percentage to increase. Finally, a good accordance between the experimental and numerical results was observed.
Keywords: Blank Holder Force, Deep drawing, Finite Element Analysis, Thickness Distribution -
Pages 59-66
In the present paper investigation is carried out to study pitting corrosion rate of Pulsed Current Micro Plasma Arc welded AISI304 and AISI430 dissimilar joint in three different mediums namely 0.5N NaOH, 3.5N NaCl and 0.5N HCl. Linear Polarization method is used and Tafel are drawn, from which corrosion rates are evaluated in Heat Affected Zone (HAZ) of AISI 304, AISI 430 and at Fusion zone (FZ) of the weld joint. Corrosion pits are studied using Scanning Electron Microscope (SEM) images. It is revealed that AISI 304 is subjected to more corrosion when compared to AISI 430. Corrosion rate is higher in HCl when compared to NaCl and NaOH mediums. Corrosion rate is high at FZ, than HAZ of AISI 304 and AISI 430.
Keywords: AISI 430, AISI 304, Micro Plasma Arc Welding, pitting corrosion -
Pages 67-74One of the most important problems in the welded Joints is the low fatigue strength due to the residual stresses. Purpose of this study is to investigate the effect of residual stresses on S/N diagram of the welded joints. For this purpose, welding process of two plates is firstly modeled on a precise and three-dimensional model. This simulation has been carried out in two non-coupled thermal-mechanical steps, including the birth and death of elements technique, presence of molten flow inside melting pool and latent heat generated by phase transformations in the simulator program. Thermal and mechanical results of the program are compared with numerical and experimental results of other researchers, which indicates acceptable accuracy of the program. In the next step, effect of welding process residual stress on S/N diagram is investigated with two different fatigue criteria, which the results indicate a decrease in the fatigue strength. Goodman's modified fatigue criterion shows 88%, and Gerber's criterion shows 78% of reduction. Finally, by examining effect of changes in air flow parameters and preheating, the results showed that the transient air flow reduced fatigue strength for 5% and preheating, results in a 9% increase in fatigue strength.Keywords: Fatigue Criteria, Residual stress, S, N Diagram, Welding Process
-
Pages 75-82
Barrel finishing is a common technique for surface finishing of industrial parts. Many factors such as working time, abrasive media, initial roughness and machining parameters of rotary barrel affect the final surface roughness of workpieces. Analysing these input parameters in order to obtain the least surface roughness as well as the least working time for barrel finishing of the specific samples, is not possible except by applying Design of Experiments method. Thus, the aim of the present paper is to improve the surface quality of the steel alloy CK45 samples in barrel finishing process, by investigating different combination of three abrasive particles including ceramics, steel balls and aluminium oxide as the abrasive media through design of experiments method. Initial roughness, working time and the combination of abrasive media are the input factors in the designed experiments, while the surface roughness is the output factor. Results show that the best surface roughness and working time have been achieved with the specific combination of steel balls and aluminium oxide particles as the abrasive media.
Keywords: Abrasive Media, Barrel finishing, Design of Experiments, Mass finishing, Surface Roughness -
Pages 83-90Most of SCARA (Selective Compliance Articulated Robot Arm) direct drive robots today are equipped with a circular feedback system. The Resolved Motion Rate Control (RMRC) method increases the accuracy and compensates the lack of movement transmission system in accurate pick and place actions. In this study, a pick-and-place SCARA robot is developed by using a developed robot manipulator arm and controlling with its designed control systems. To make the end-effector of the SCARA robot arm following desired positions with specified joint velocities, the inverse kinematics technique, known as the RMRC generates motion trajectories automatically. In this research, the kinematics method has been applied with the Jacobian pseudo-inverse or Jacobian singularity-robust inverse to generate and record the pick-and-place motion of the SCARA robot. These records are then compared with the records after using RMRC methods. Several system features like the variation of samples during 50 seconds for the first and second robot joint, and mean deviation for the detailed analysis by the controller after using RMRC motion control algorithm demonstrates the preference of RMRC method in SCARA direct drive robots.Keywords: Direct Drive, Resolved Motion Rate Control, robotic, SCARA
-
Pages 91-97In the present study, resistance upset butt welding was used as a solid-state process for joining Ti-6Al-4V alloy. Results showed that melting and subsequent solidification of the alloy at the joint interface promoted the development of a cast microstructure along with some pores. However, by applying the constant upset pressure of 1.62 MPa, the pore volume fraction decreased considerably with decreasing the welding current from 110 A/mm2 to 55 A/mm2. Hardness test results showed that the weld interface and the base material had the highest (352 HV) and the lowest (318 HV) values, respectively. The microstructure of the interface consisted of ά martensite and Widmanstätten laths. The tensile strength of the joints varied between 550 and 883 MPa depending on the welding parameters used. In the optimum condition, the maximum strength of the joint was about 94% of the base metal strength. Fractography of samples confirmed that the formation of pores deteriorated the strength of the joints.Keywords: Fractography, Microstructure, Solid-State Welding, Ti-6Al-4V Alloy, Weld Defect
-
Pages 99-105Chatter is one of the most limitations that cause undesirable effect on improving productivity and part quality. In this paper, an experimental method has been used for analysing the effect of changing pitch in the indexable cutting tool in milling. For this purpose, the cutting forces of machining in three different directions were investigated and a comparison was made between tools with equal and unequal pitches. Milling of AISI 4140 has been performed with two different depths of cut (0.5&1mm) and the machining surface finish were examined. Furthermore, by using accelerometer sensors, the machining vibrations and machining forces by using dynamometer were measured. According to the findings, as well as the reduction of vibrations of machining about 50 %, machining forces reduction between 15% and 30% and surface finish improvement more than 200%were observed. In this regard, utilizing tools with different pitches leads to improvement in machining efficiency, reducing energy consumption, manufacture of high quality parts and it will ultimately reduce costs.Keywords: Machining Efficiency, Milling, Chatter Phenomenon, Tools with Different Pitch