فهرست مطالب
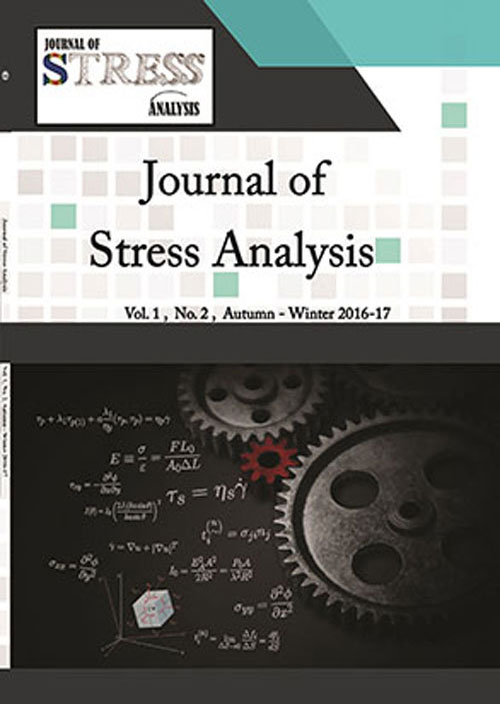
Journal of Stress Analysis
Volume:5 Issue: 2, Autumn-Winter 2020-21
- تاریخ انتشار: 1400/04/02
- تعداد عناوین: 12
-
-
Pages 1-10In this paper, energy absorbing characteristics of aluminum/polypropylene/steel sandwich cups are investigated. To this end, sandwich panels were fabricated using hot pressing technique. Then the panels were deep drawn using a circular punch to produce three-layer cups. Subsequently, the cups were axially compressed (crushed) under quasi-static deformation in order to investigate their energy absorption capacity. Finally, the effects of thickness of polypropylene layer as well as circular cutout triggers on energy absorption of the sandwiched cups were evaluated. The results show that changing the thickness of polypropylene layer from 1 to 2mm could successfully increase the energy absorption by about 24%. Furthermore, adding geometrical triggers like circular cutouts with radius of 2.5 mm could reduce the absorbed energy from 346J in the sample without trigger to about 335J in the sample with trigger (3.2% reduction). The trigger could also reduce the peak force near 14% (from about 29kN to about 26kN) that can be considered as a positive point of triggers to mitigate damage in the samples.Keywords: Deep drawing, Sandwich Panel, Composite, energy absorption, Geometrical
-
Pages 11-20The aim of this work is providing a suitable method based on the theory of critical distance (TCD) to estimate the fatigue life of notched components in the presence of residual stress induced by the overload cycle. Presented method is relied on a virtual stress field to equalize the effects of real stress distribution in the hot spot around the notch root. This method is noted as equivalent virtual stress (EVS) method. The EVS method combined with some versions of the TCD method, such as the point method (PM) and line method (LM), were applied for two types of notched samples. Samples were made with U- and V-notches with axial stress concentration factors as 2.45 and 5.55, respectively. The test material was AA 2024-T3 due to its considerable resistance to fatigue failures. The PM was found more conservative, while LM showed more accuracy, especially when the critical distance parameter locates far from critical regions. A good agreement was observed between experimental and predicted results.Keywords: Notch, Fatigue life, Overload, Theory of critical distance, Point, line methods
-
Pages 21-31Equal-channel angular pressing (ECAP) is an efficient process to produce bulk nanostructured materials, in which a large amount of strain can be imposed on the workpiece via multiple passing deformations without changing its dimensions. In this study the distribution of induced strain was analytically modeled by correlating the Cartesian coordinates with inclination angle (α) and polar angle (θ). The effects of die angles and the routes A and B (without and with rotation 90◦ around the billet axis) were evaluated. The results indicated that the degree of strain rate for the inner corner was three times higher than that of the outer corner. In deformation via route A, the degree of strain rate for θ changed from pass to pass, but for α was the same for all the applied passes. In comparison, when the sample was subjected to deformation through route B, the strain distribution patterns altered from pass to pass. For route B, the maximum value of the inhomogeneity index was approximately 1.5 times less than that of route A.Keywords: Analytical modeling, ECAP, Shear strain, plastic deformation, Route
-
Pages 33-40Laser bending process of a circular tube made of mild steel was investigated with experimental tests and finite element simulations. The effects of main process parameters such as laser output power, laser scanning speed, and laser beam diameter on the main and lateral bending angles of laser-bent tube were studied. The experimental tests were performed with a continuous CO2 laser. The numerical simulations were carried out with Abaqus/Standard technique. The finite element simulations were compared with experimental measurements by adjusting the absorption and heat transfer coefficients of the heat flux in the numerical simulations and comparing the obtained temperature profiles with experimental results. The accuracy of numerical simulations was proved by comparing the numerical results with experimental measurements. The obtained experimental and numerical results showed that increase in the laser output power leads to an increase in the main and lateral bending angles. Moreover, the results proved that the main and lateral bending angles increased with decreasing the laser scanning speed and laser beam diameter.Keywords: Laser tube bending, Main bending angle, Lateral bending angle, Laser output power, Laser scanning speed, Laser beam diameter
-
Pages 41-52For the first time, the fracture toughness of pipeline with outer diameter of 168.3mm (thickness: 6.9mm; grade: API X46) was determined using the J-integral (according to ASTM standard E1820), single edge bend [SE(B)], and single-specimen method. The pre-crack was created using fatigue and the crack propagation was measured using the unloading compliance method. In each stage of crack propagation, the J-integral parameter was calculated and JQ was obtained using the J-R curve. The results indicated that satisfied the test’s validity criteria, and was equated to JQ. Subsequently, KIC was gained from the relationship between JIC and KIC. For the given pipeline, JIC and KIC were equal to 51 kJ/m2 and 105.4MPa√m, respectively. In addition, assessment of longitudinal cracks with different depths and lengths on the pipes body was conducted using fracture toughness and Failure Assessment Diagrams (FADs) for levels one and two of BS7910 standard. Results showed that a longitudinal crack with a depth of 5mm and a length of 220mm lies in the safe zone.Keywords: fracture toughness, Single edge bend, Single specimen method, J-integral, Failure Assessment Diagrams
-
Pages 53-61Twin Parallel Channel Angular Extrusion (TPCAE) is a newly presented severe plastic deformation (SPD) technique in which two specimens can be processed simultaneously. This method is capable of processing more volumes of materials in addition to less energy consumption. In the present work, stress analysis of tools in this method was conducted using DEFORM 2D finite element software package. Moreover, in order to compare the results with the stress configuration in the conventional Equal Channel Angular Extrusion (ECAE) process in parallel channels, named Single Parallel Channel Angular Extrusion (SPCAE), stress analysis was also conducted with the same processing condition as TPCAE simulation. The results illustrate that TPCAE is a method with lower magnitudes of stress concentrations in the die and lower overall stress magnitudes in the punch with respect to the SPCAE. In addition, it was found that on the contrary to SPCAE, there is a symmetrical stress distribution in the punch and die in TPCAE, bringing about more lifetime for this method.Keywords: Finite element method, Severe plastic deformation, Die stress
-
Pages 63-72Austenitic stainless steels are commonly used in low temperature applications because of their mechanical properties specially preserving the ductility. The strain-induced martensitic transformation greatly affects the plastic behavior of the metastable austenitic stainless steels. This paper provides a simple constitutive model for considering the strain-induced martensitic transformation of the metastable austenitic stainless steels at low temperature. A modified kinetics model is represented to consider the effect of TRIP in martensite evolution explicitly. In addition, a modified power law hardening for the continuously reforming material is represented to describe the great hardening effect of the phase transformation. Developing an incremental integration algorithm, the constitutive model was implemented in the Abaqus/Standard via a user-defiened material subroutine (UMAT). The results showed that the rate of martensite evolution with plastic strain in the modified model is accelerated which significantly affects the plastic behavior. In addition, the hardening behavior could be well described with the modified power law. Numerical examples show the capability of the constituative model in simulating the strain-induced transformation at low temperatures.Keywords: Austenitic Stainless Steel, Strain-induced Martensitic Phase Transformation, Constitutive Model, Low Temperature, Plasticity
-
Pages 73-82Today the adhesively bonded joint of FRP/steel for repair and strengthening are being widely used. In this case, investigating the effect of various mechanical loading, as well as harsh environmental conditions on this joint, is very important. In this paper, the strength of the damaged-steel plate reinforced with CFRP patches under acidic environment is investigated experimentally. The damage is considered in the shape of a central hole with two narrow central notches on two sides of the hole. In order to simulate more realistic conditions, the bonding of the patch to the steel plate is considered one-sidedly. To evaluate the amount of strengthening, the specimens are subjected to the simple tensile test at room temperature. The results of dry patched-specimens compared to non-patched specimens show significant reinforcement with at least 40% increase in load-carrying capacity and at least 50% increase in displacement. The comparison between the patched-specimens immersed for 8 weeks in concentrated sulfuric acid and the dry patched-specimens show no significant effect on the load-carrying capacity. However, the tests of standard CFRP specimens in a similar immersion environment show a reduction in modulus of elasticity and tensile strength compared to the dry CFRP ones.Keywords: CFRP patch, Damage steel plate, Adhesively bonded joint, Acidic environment, Tensile behavior
-
Pages 83-99
The production of fine-grained materials by Severe Plastic Deformation (SPD) methods has made these methods more attractive. The basic condition for producing specimens with better mechanical properties and more homogeneous structure is the application of high and uniform plastic strain. Many researchers have tried to modify the existing SPDs or introduce new techniques to achieve these goals. In this research, in order to improve the mechanical properties of the specimens, a new method is introduced, which is the combination of the two processes of torsional extrusion and ECAP. Then, by performing the design of experiments, the optimal die geometric parameters, including the internal angle of the ECAP channel α, the outer angle of the ECAP channel , the length of the torsional region L, the ratio of large diameter to small diameter of the ellipse, m, and the torsional angle of the elliptical section, θ, were obtained 90.5◦, 39◦, 34mm, 1.65 and 120◦, respectively.
Keywords: Severe plastic deformation, Equal channel angular pressing, Torsional Extrusion, mechanical properties -
Pages 101-108In this paper, energy absorption of aluminum thin-walled combined geometry, including a cylinder and a hemisphere under axial and oblique loading, is investigated using numerical simulation. The aim of this research is optimizing the dimensions of the combined geometry in order to increase the energy absorption capacity and comparing it with an equal weight thin-walled simple cylinder. Numerical simulations were performed at 0, 7, 14, and 21 degree of loading using ABAQUS software. The results showed that with increasing the radius of curvature and decreasing the height of the combined geometry, energy absorption parameters increase, and in general the combined geometry has better performance than the simple cylinder especially in oblique loading. The SAE and CFE of the optimum combined geometry with dimensions of R = 25mm, h = 25mm, H = 181:92mm, and D = 50mm in the 0 and 7 degree of loading is similar and in the 14 and 21 degree of loading increased 300% and 200% respectively in comparison with an equal weight thin-walled simple cylinder.Keywords: energy absorption, Thin-walled, combined geometry, axial, oblique loading, Aluminum
-
Pages 109-122In this work, the spectral collocation method based on Chebyshev polynomials is developed and utilized for analysis of static, free vibration, and dynamic behavior of one and two-dimensional solid structures. The main objective of the work is to introduce the spectral collocation method with Chebyshev polynomials as a powerful numerical method for solid mechanic analysis. To show the advantage and effortlessness of this method, one and two-dimensional solid structures as case studies were considered and the spectral collocation method was directly applied to the analysis and the governing equation was solved. Moreover, the homogeneous material properties and functionally graded material properties were analyzed to show the capability of the introduced method for solving the more complicated equations of motion. The results obtained for each case were compared with analytical and numerical results presented in the literature and some results were also compared with ANSYS. The results showed that the presented method has very good accuracy and efficiency to solve structural-mechanical properties.Keywords: Chebyshev polynomials, Structural analysis, free vibration, dynamic analysis
-
Pages 123-135
In the present study, the Charpy impact test was performed on 7075-T651 Aluminum alloy specimens with different notch angles for fracture energy measurement. In this regard, specimens with seven different notch angles were prepared, and then fracture energy was measured using the Charpy impact test. By considering the experimental results a quadratic relationship between the fracture energy (CVN in J) and the notch angle of the Charpy specimens was achieved for the tested Aluminum alloy, so the fracture energy of the 7075-T651 AA specimens was calculated for each desired notch angle. The experimental data validation was performed using mathematical modeling. Furthermore, the fracture surface of the specimens was investigated at different notch angles using SEM. By increasing the notch angle to the standard specimen, the fracture surface becomes smoother and tends to feature a brittle fracture as well as the shear lip is reduced. Moreover, for the specimens with higher notch angle (from the standard), the fracture surface tends to feature a ductile fracture and the shear lip increases.
Keywords: Fracture energy, 7075-T651 Aluminum Alloy, V-shaped notch, Notch angle, Charpy impact test