فهرست مطالب
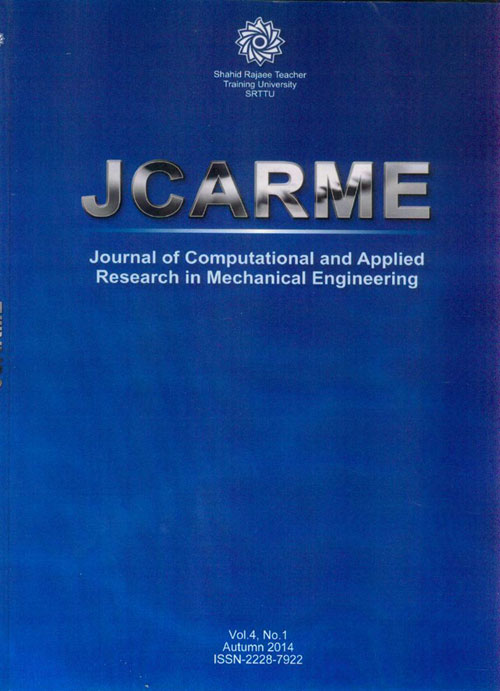
Journal of Computational and Applied Research in Mechanical Engineering
Volume:4 Issue: 1, Autumn 2014
- تاریخ انتشار: 1393/03/27
- تعداد عناوین: 7
-
-
Page 1In this paper, three-dimensional modeling of the fatigue crack growth profiles was performed in a simple riveted lap joint. Simulation results showed that mode I was dominated on the one side of the plates and the crack straightly grew on this side, while the other side of the plates was in a mixed-mode condition and the crack propagation path was not straight on this side.Afterward, the fracture mechanics-based life prediction of the riveted lap joint was considered using EIFS concept. Back extrapolation method was used for estimating EIFS. Results demonstrated that EIFS would depend on loading amplitude if ΔK had been implemented in EIFS estimation using Paris equation. In contrast EIFS dependency on loading amplitude significantly reduced when using ΔJ in EIFS estimation. Finally, fatigue life of the riveted lap joint was predicted based on safe life method using Brown-Miller critical plane criterion. Results represented that the predicted life using fracture mechanics concept was much closer to the experimental results.Keywords: Riveted Lap Joints, Fatigue Crack Growth Profiles, EIFS, Life Prediction
-
Page 19An analytical study was performed to study effects of thermo-diffusion and chemical reactions on a three-dimensional MHD mixed convective flow of dissipative fluid along an infinite vertical porous plate with transverse sinusoidal suction velocity. The parabolic partial differential equationsgoverning the fluid flow, heat transfer, and mass transfer were solved using perturbation technique and the expressions for velocity, temperature, and concentration distributions were obtained. Expressions for skin friction at the plate in the direction of the main flow, rate of heat transfer, and mass transferfrom the plate to the fluid were derived in a non-dimensional form. Velocity,temperature, concentration, amplitudes of the perturbed parts of skin friction, rate of heat transfer, rate of mass transfer, and skin friction at the plate are presented in graphs and effects of various physical parameters like Hartmann number M, Prandtl number Pr, Reynolds number Re, Schmidt number Sc, Soret number So, Grashof number for heat transfer Gr, Grashof number for mass transfer Gm, and chemical reaction parameter Kr on the above flow quantities were analyzed and then the obtained results were physically interpreted.Keywords: Convection, Magnetic field, Heat transfer, Mass transfer, Chemical reaction, Thermo diffusion
-
Page 43Existence of cracks in industrial structures is one of the important causes of their failure, especially when they are subjected to important axial compressive forces that might lead to buckling. Therefore, it must be considered in stress analysis and designing and loading of such structures. In this paper, the buckling and post-buckling behaviors of stainless-steel cracked plates under axial compression load were investigated both experimentally and numerically and effects of the geometrical and mechanical parameters, such as crack length, crack angle, crack position, plate imperfection, load band, and plate thickness on the critical buckling load were studied. In the experimental study, mechanical properties and plastic behavior of stainless steel plates were determined for the subsequent numerical study. Numerical modeling was carried out by ABAQUS finite element software. Numerical predictions were compared with the experimental results and the reliability of the numerical solution was proven. Results demonstrated the considerable effects of the mentioned parameters on the critical buckling load of plate.Keywords: Cracked plate, Buckling, Post, buckling, Experimental method, FEM
-
Page 55In this paper, nonlinear equations of motion for laminated composite rectangular plates based on the first order shear deformation theory were derived. Using a perturbation method, the nonlinear equation of motion was solved and analytical relations were obtained for natural and nonlinear frequencies. After proving the validity of the obtained analytical relations, as an alternative and simple modeling technique, ANN was also employed to model the laminated rectangular plates and predict effects of different parameters on the natural and nonlinear frequencies of the plates. In this respect, an optimal ANN was selected and trained by training data sets obtained from analytical method and also tested by testing data sets. The obtained results were in good agreement with the analytical and published results.Keywords: Nonlinear vibration, Simply, supported, Rectangular laminated plates, Artificial neural Network
-
Page 67Laser forming is a modern process which is mainly used for forming metals. Different Lasers are used in this regard that includes Nd: YAG and CO2. In this study, forming bi-layer sheets of Aluminum/Ceramic by Laser was investigated. Furthermore, effect of Uniform and Gaussian heat flux distribution in different power, velocity, and beam diameters on bending angle was studied. FEM simulation indicated that, in the same conditions of analysis, Uniform heat flux distribution caused higher bending angle than Gaussian heat flux distribution. Moreover, the results showed that there was an optimum point at different speeds and laser beam diameters, at which the bending angle was maximum. In order to evaluating the numerical results, a set of experiments was conducted, which showed good agreement.Keywords: Laser Forming, Cermet, Gaussian distribution, Uniform distribution
-
Page 81This study focused on the optimization of Al—Mg to CuZn34 friction stir lap welding (FSLW) process for optimal combination of rotational and traverse speeds in order to yield favorable fracture load using Grey relational analysis (GRA). First, the degree of freedom was calculated for the system. Then, the experiments based on the target values and number of considered levels, corresponding orthogonal array, Grey relational coefficient and Grey relational grade were performed. In the next step, Grey relational graph of each level was sketched. The performed graph and analysis of Grey results proved the impact of rotational speed and traverse speed on fracture load of resultant joints. Finally, the optimum amount of each parameter for better strength of the welds was obtained. This study showed feasibility of the application of Grey relational analysis for achieving dissimilar friction stir lap welds with the highest quality.Keywords: FSLW, Dissimilar, Optimization, Grey relational analysis
-
Page 89Jet impingement heat transfer is an effective and practical approach that is employed in many industrial processes where heating, cooling, or drying is required. Details of the heat or mass transfer rate have been investigated bothexperimentally and numerically and can be found in the published literature. In most of the numerical studies, control-volume approach has been employed to solve the governing equations of the thermal and flow fields. Using this numerical approach, a pressure correction equation is usually developed from the conservation equations in a rigorous manner to obtain the pressure distribution. Avoiding the complexities encountered in the traditional manner, a full implicit finite-difference method was developed for the first time and applied for studying jet impingement heat transfer. Similar to the velocity components, static pressure was also treated as an unknown variable in this approach. Specifications of both flow and thermal fields were obtained for two cases of confined and unconfined jets by the proposed numerical method. It was demonstrated that this novel numerical approach was a straightforward method, which required no additional equation for pressure calculation, and had the potential use in other two- or three-dimensional flow and thermal field analysis.Keywords: Finite, difference method, Numerical model, Impingement heat transfer, Jet impinging