فهرست مطالب
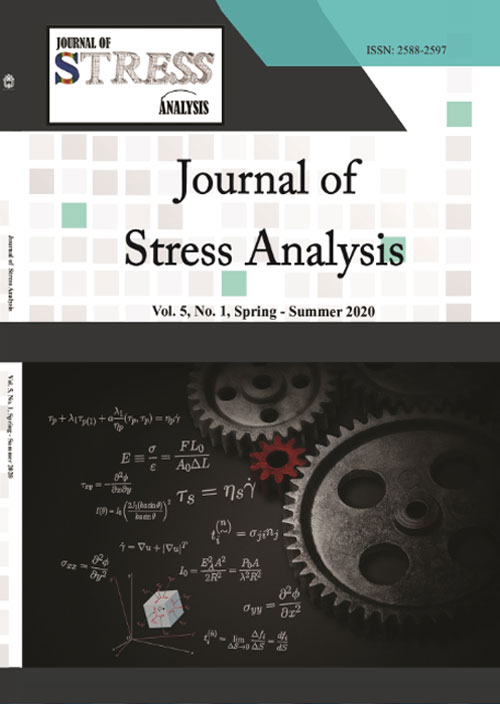
Journal of Stress Analysis
Volume:6 Issue: 2, Autumn-Winter 2021-22
- تاریخ انتشار: 1401/08/04
- تعداد عناوین: 12
-
-
Pages 1-19In this paper, the thermo-mechanical buckling analysis of a non-homogeneous open cylindrical shell reinforced with single-walled carbon nanotubes with a uniform/non-uniform distribution on an elastic foundation under thermal andmechanical loads has been addressed. Using the minimum energy principle, the governing differential equations of this system are derived and in order to determine the properties of the reinforced composite shell, the modified mixtures law has been used. It is assumed that the properties of single-walled carbon nanotubes are acquired from molecular dynamics simulation. It is also assumed that the material properties of the reinforced carbon nanotube composites are linear in the thickness and are defined based on mixture law via a micro-mechanical model in which the nanotube performance parameter is considered. After solving these equations, the effects of geometric characteristics of the shell and material properties on the critical load and critical temperature of shell buckling are investigated.Keywords: Mechanical buckling, Thermal buckling, open cylindrical shell, carbon nanotubes, third-order theory of shear deformation
-
Pages 21-29For the Resistance Spot Welding (RSW) process, the effects of Welding Current (WC), Electrode Force (EF), Welding Cycle (WCY), and Cooling Cycle (CCY) on the Tensile-Shear Strength (TSS) of the joints have been experimentally investigated. An Adaptive Neural-Fuzzy Inference System (ANFIS) based on data taken from the test results were developed for modelling and predicting of TSS of welds. Optimal parameters of ANFIS system were extracted by Gray Wolf Optimization (GWO) algorithm. The results show that ANFIS network can successfully predict the TSS of RSW welded joints. It can be concluded that the coefficient of determination and mean absolute percentage error for the test section data is 0.97 and 2.45% respectively, which indicates the high accuracy of the final model in approximating the desired outputs of the process. After modeling with ANFIS-GWO, the effect of each input parameter on TSS of the joints was quantitatively measured using Sobol sensitivity analysis method. The results show that increasing in WC, WCY, EF, and CCY leads to an increase in TSS of joints.Keywords: Resistance spot welding, Adaptive neural-fuzzy inference system, Gray wolf optimization algorithm, Sobol sensitivity analysis method, AISI 304 steel
-
Pages 31-46In this article, the changes in High-Cycle Fatigue (HCF) lifetimes of the AZ91 magnesium alloy are investigated under the influences of the different heat treatments and also the Rare-Earth (RE) element addition. For this purpose, some different heat treatments, including a common solution treatment, with different ageing treatments and RE elements were performed. Then, the sensitivity analysis was done using the regression analysis by the DESIGN EXPERT software on the experimental data. At a similar fatigue lifetime, the RE element increased the strength or the stress level by at least 30%, and also, the RE element with heat-treating enhanced the material strength by at least 50%. The results of sensitivity analysis on the experimental data illustrated that the stress level, the heat treatment, and the RE element (RE) were the most effective parameters on the fatigue lifetime, respectively. Besides, the fatigue lifetime was sensitive to the interaction of the heat treatment and the RE element. In addition, the fracture surface analysis demonstrated that allsamples had three different zones for the crack initiation, the crack growth, and the sudden final fracture.Keywords: Sensitivity analysis, Magnesium alloys, Heat treatment, Rare-earth element, Fatigue lifetime
-
Pages 47-57Accuracy in determination of mechanical properties in industrial parts is a major issue in engineering. Various methods have been introduced to estimate the mechanical properties of the industrial parts, and each has its own features and limitations. The present research investigates the accuracy of Instrumented Indentation Technique (IIT) with Kim’s model in determining mechanical properties, including elastic modulus, yield stress, and work hardening of the A516 steel samples having surface stresses. To this end, some 3D simulations, using IIT on the steel sample with different surface stress state, were performed, and the method’s error in comparison to the initial assumed values were obtained. The results show that the surface stresses significantly affect the error in determining the materials’ properties, and the error in samples with tensile surface stress is more than that of samples with compressive one. To validate the results, some experimental samples with specified initial stress were prepared, which measured mechanical properties by the IIT and then were compared with the tensile test results.Keywords: mechanical properties, Surface Stress, Instrumented Indentation Technique, Measurement Accuracy
-
Pages 59-65Finding a way to reduce the wear resulted from aperities interactions in mixed lubrication regime is an interesting area. One of the inspiring solution is surface texturing. Using a convenient laser, a textured surface with arbitrary micro cavity shape and size was prepared accurately. In this study, the effect of laser surface texture on the wear and friction behavior of discs in line and point contact in mixed lubrication regime was investigated. The effect of texturing area, linear velocity, and vertical load were examined. The friction coefficient variation reaches a narrow margin after an adequate distance. The results showed that wear decreases with increasing speed and decreasing the applied force. Comparing the results between plane and textured discs, it was found that the coefficient of friction was reduced between 12 and 19% and theamount of wear was reduced by almost more than 40%.Keywords: Lubrication, Elastohydrodynamic, Friction, Wear, Surface Texture, Laser
-
Pages 67-74Eliminating the need for external manipulation due to the ability of hydrogels to sense the environmental stimuli and swelling, makes it suitable for sealing applications. As the matter of fact, many researchers from both academia andindustry have investigated hydrogel seals experimentally and numerically. In this work, by using constitutive models available in the literature, the sealing properties of rectangular hydrogel seals are numerically investigated. To investigate elastic leakage of hydrogel seals subjected to fluid pressure, leakage models of elastomeric ones are implemented. The methods are validated by comparing the result of the model with available experiments in the literature. Afterward, the mechanism of leakage of hydrogel seal is presented, and then, parameter studies are carried out. It has been found that increasing the cross-link density, hydrogel length, and the ratio of hydrogel thickness to the gap it seals increases the value of fluid pressure associated with leakage.Keywords: Hydrogel, Finite element method, Elastic Leak, Seal
-
Pages 75-83The Split Hopkinson Pressure Bar (SHPB) is a commonly used technique to measure the stress-strain behavior of materials at high strain rates. Using Utilizing the strain records signals recorded in the input and output bars, the average stress, -strain and strain rate in the sample can be calculatedis determined by the one-dimensional wave propagation equations of SHPB formulas based on the one-dimensional wave propagation theory. The accuracy of a SHPB test is based on this assumption as well as dynamic equilibrium. In this paperarticlework, the possibility feasibility of using a laser measuring system to obtain the dynamic properties of a wide range ofvarious materials using split Hopkinson pressure bar without strain gages is studied. In this method which is a non-contact one, the displacements of bar/sample interfaces are measured directly using a laser extensometer technique. After designing a proper set of optical elements, the operation of the method is evaluated using numerical simulation in ABAQUS/Explicit. Cast iron, aluminum and polypropylene samples, which represent the properties of hard to soft, respectively, were studied to evaluate the proposed measurement method for different materials. The comparison with other strain gage methods shows good agreement and lower fluctuation in stress-strain curves. Moreover, since the one-dimensional wave propagation is not used in this method, we show by numerical simulation that the proposed method can be used even with shorter pressure bars which can reduce the cost of manufacturing and maintaining the SHPB apparatus.Keywords: Split Hopkinson pressure bar, Laser measurement, High strain rate, Displacement measurement
-
Pages 85-95Severe plastic deformation processes are used as a method to increase the mechanical strength of metals. One of the new deformation methods is twist channel angular pressing (TCAP). TCAP has been developed based on a combination of twist extrusion processes (TE) and Equal Channel Angular Pressing (ECAP) process. In this paper, the effect of TCAP die geometry on the grain size distribution and plasticity properties using simulation in DEFORM software is investigated. For this reason, dies with internal angles of 90◦, 100◦ and 110◦, external (corner) angles of 0◦, 10◦ and 20◦ and twist angles of 30◦, 45◦, 60◦ are used. In addition, the location of the twist channel is examined before and after the ECAP location. The distribution of plastic strain, grain size distribution, and the required punch force for the TCAP process on Aluminum alloy 7050 are extracted in all conditions. The results showed that locating the twist section after ECAP location led to a better microstructure in the billet. Also, die with a twist angle of 45◦, an internal angle of 110◦, and a corner angle of 0◦ created the best results; therefore, the grain size decreased from 100µm to 3.67µm.Keywords: TCAP, Sever plastic deformation, ECAP, Microstructure, Aluminum alloy
-
Pages 97-105In this paper, a semi-analytical model was proposed to superimpose the initial residual stress components on the work roll surface and subsurface to minimize the maximum value of Von-Mises Stresses (MVMS) during the hot rolling process to reduce the possibility of roll wear and increase the fatigue life. A Finite Element Model (FEM) was proposed to assess the temperature and thermomechanical stress in work roll during hot rolling. An analytical method was developed to implement the three initial residual stress components designed by the full factorial analysis of variance (ANOVA) method in the obtained FEM thermomechanical stress results. An Artificial Neural Network (ANN) was used to establish an objective function to relate the initial residual stress components to the MVMS. Subsequently, the single and multi-objective Genetic Algorithm (GA) optimization were used to find the optimal value of initial residual stress components to minimize the MVMS on the surface and subsurface of the work roll. The results showed a significant reduction of boththe value and amplitude of the MVMS on surface and subsurface of a work roll during the hot rolling process.Keywords: Residual stress, Von-Mises stress, Design of experiment, Artificial neural network, Genetic Algorithm, Optimization, Hot rolling
-
Pages 107-116Few analytical approaches have been proposed so far for solving FluidStructure Interaction (FSI) problems in the literature. In fact, FSI is generally so complicated that its analytical solution remains almost unavailable. Inspired by this fact, here an analytical methodology is presented for modeling steady-state fluid-structure interaction problems in axisymmetric domains. For this purpose, the Navier-Stokes equations for the flow of the incompressible viscous fluid, and the linear elasticity equations for the deformation of the solid structure are expressed in axisymmetric coordinates. Appropriate boundary conditions are also employed that are capable of coupling the fluid and solid domains by imposing kinematic and dynamic constraints on the fluid-structure interaction interface. The set of fluid and structure equations are solved by MATLAB symbolic toolbox. The accuracy of the presented analytical approach is verified in two different ways. First, by specializing the results for the simple case of a thick cylindrical pressure vessel, second, by comparing the analytical results for flow through a nozzle with numerical results obtained by ANSYS/CFX simulation. Variation of the stress components is obtained in the nozzle wall. The results of the analytical approach are in good agreement with those of the numerical modeling. The proposed methodology can be used for fast yet efficient solution of fluid-structure interaction problems in axisymmetric configuration.Keywords: Fluid-structure interaction, Analytical solution, Axisymmetric domain, Stress variation
-
Pages 117-122Titanium (Ti) has poor tribological and mechanical properties such as low hardness and wear resistance. In this study, we considerably improve Ti’s hardness by laser ablation method. Ambient air, N2 gas chamber and N2/liquid water environments were separately selected as irradiation environments and their effect was comparatively studied on Ti treatment surfaces. The fabrication of titanium nitride (TiN) structure was successfully confirmed by XRD analysis in N2 gas and N2/liquid water as irradiation media. Accordingly, there was good adhesion between TiN structure and Ti’s surface. Vickers hardness test indicated the laser treatment and TiN structure significantly improved Ti’s hardness. The formed TiN structure in N2/liquid water environment had the highest hardness value of 530Hv comparing to hardness of ablated Ti in N2 gas (370Hv) and air (340Hv). The escalation of Ti hardness and generation of TiN structure with lasertreatment in N2/liquid water environment is a favorable aspect of this method.Keywords: Microhardness, Surface treatment, Laser ablation, Titanium nitride, Fiber laser
-
Pages 123-130This paper investigates the quasi-static compressive strength of two sandwich structure designs in which cores consist of trapezoidal corrugated panels. In one design, the core consists of a steel cross-corrugated two-layered structure, while in the other design, the core consists of a single layer of bidirectional interconnected corrugated core made of ST37 steel sheets. To investigate the energy absorption capacity of these sandwich structures quasi-static compression is performed numerically and experimentally. First, from each design, a test specimen is constructed and tested under quasi-staticcompressive load. Following that, the finite element models of the designs are constructed and their crushing process is simulated and the FEM method results were compared with the test results and the FE model is verified. After verification of the numerical model, for each design, three different trapezoidal wave profiles are modeled and, the mechanical behavior of the other bidirectional interconnected corrugated cores is evaluated numerically. The results showed that the maximum force and energy absorption capacity of the sandwich structures with the single-layered bi-directional interconnected corrugated core is higher than the strength and energy absorption capacity of their counterparts with the same weight in the two-layered bi-directional corrugated core group with the same weight. It was also found that, inthe single-layered bi-directional interconnected corrugated core group, the failure mode is plasticity near the welding joints, while for the single-layered bi-directional interconnected corrugated core, the failure mode is plastic buckling of the corrugated core under compressive load and some local plastic deformation in the connection of the layers.Keywords: Mechanical energy absorption, Crushing, Quasi-static compression, Two-layered bi-directional corrugated core, Single-layered bi-directional interconnected corrugated core